shed plan
Friday, November 22, 2024
Free Pallet Shed Plans: Build a Strong, Budget-Friendly Shed for Your Yard
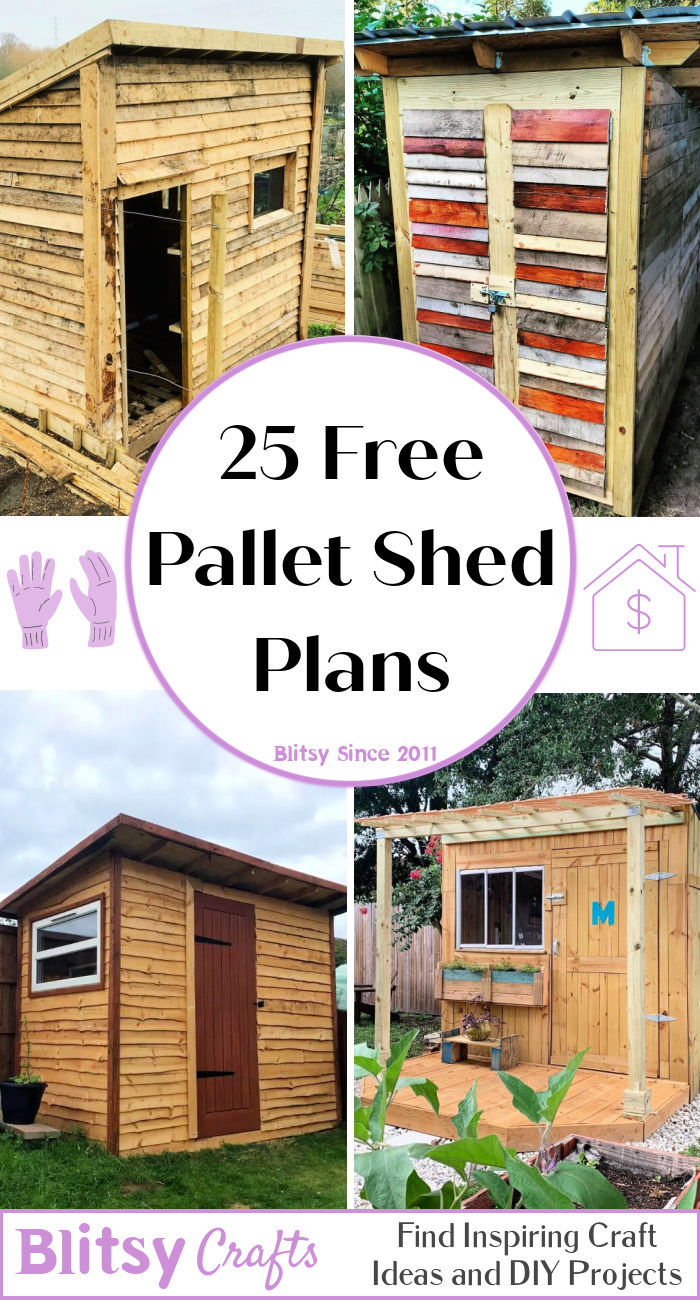
Free Pallet Shed Plans: Build a Strong, Budget-Friendly Shed for Your Yard Tired of overflowing garages and cluttered yards? Yearning for extra storage space without breaking the bank? Then look no further! This guide provides you with free pallet shed plans, empowering you to build a sturdy and stylish storage solution using reclaimed materials. Transform discarded pallets into a functional and attractive addition to your property, all while [...]
Thursday, November 21, 2024
Create a Strong Pallet Shed DIY for Your Backyard with These Simple Plans
Build a Strong Pallet Shed: Your Backyard's New Storage Solution Tired of clutter piling up in your backyard? Dreaming of a neat and organized space to store your gardening tools, outdoor furniture, or seasonal decorations? Then build your own pallet shed! This DIY project is surprisingly achievable, even for novice builders, and offers a fantastic blend of rustic charm and practical storage. This guide will walk you through the process, ensuring [...]
Build a Pallet Shed for Garden Storage with These Simple Plans

Build Your Dream Pallet Shed: A Simple Guide to Garden Storage Bliss Hey there, fellow gardening enthusiasts! So, you're looking to build a shed, huh? And not just any shed, a *pallet* shed! Smart move. They're cheap, surprisingly sturdy, and offer a really charming, rustic look. This guide will walk you through building your own pallet shed for garden storage, from start to finish. Don't worry, I'll keep it simple and straightforward â€" [...]
Wood Pallet Shed Build: Transform Old Pallets into Your Dream Shed
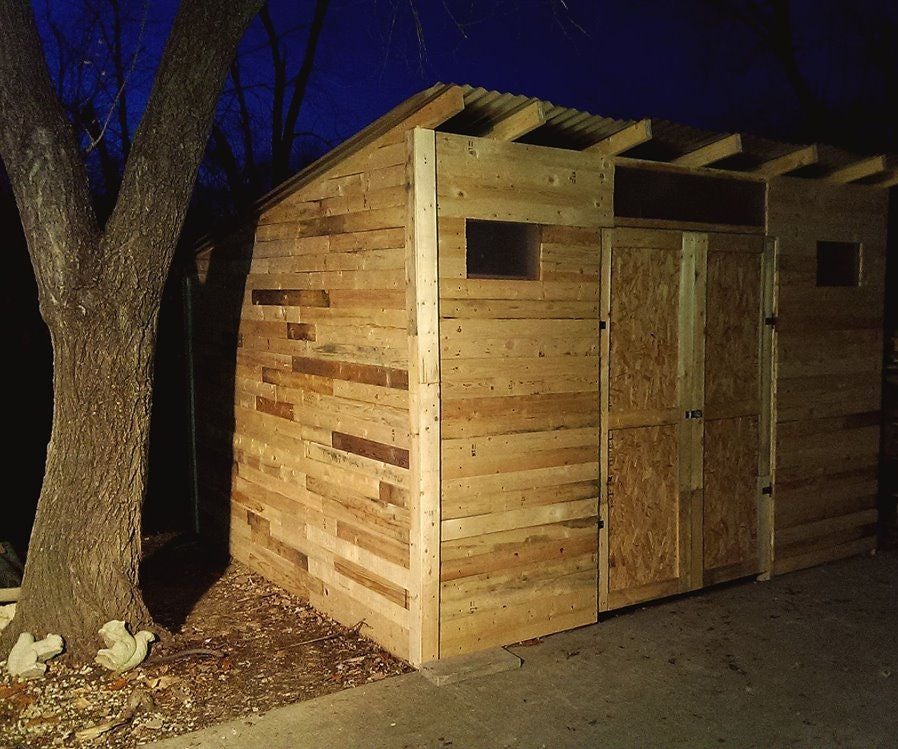
Wood Pallet Shed Build: Transform Old Pallets into Your Dream Shed Hey there, fellow DIY enthusiasts! Ever looked at a stack of old wooden pallets and thought, "I could build something amazing with those"? Well, you're in the right place! This guide will walk you through building your own shed using reclaimed pallets, saving you a ton of money and giving you a seriously cool project to brag about. Let's get started on transforming those humble [...]
Step-by-Step DIY Pallet Shed: Quick and Easy Plans for Beginners
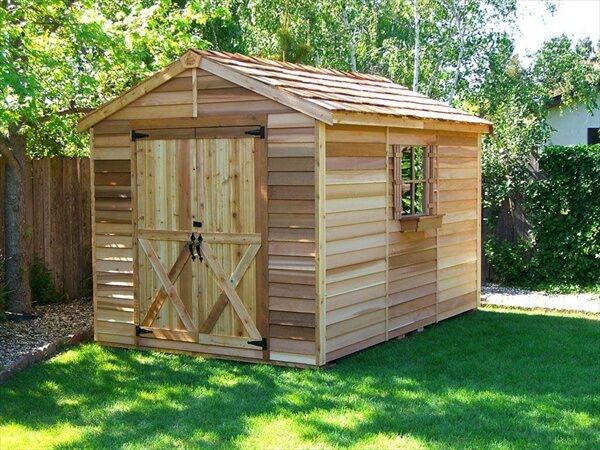
Step-by-Step DIY Pallet Shed: Quick and Easy Plans for Beginners Constructing a shed can be a daunting task, often requiring extensive carpentry skills and significant financial investment. However, this comprehensive guide offers a simplified approach to building a functional and aesthetically pleasing shed using readily available reclaimed pallets. This project is designed for beginners, emphasizing ease of construction and minimizing the need [...]
How to Build a Lean-To Shed DIY: Simple Plans for Sustainable Storage

Building Your Own Lean-To Shed: A DIY Guide to Sustainable Storage Hey there, fellow DIY enthusiasts! So you're thinking about building a lean-to shed? Fantastic! It's a rewarding project that's surprisingly easier than you might think, and the sense of accomplishmentâ€"plus the extra storage spaceâ€"is unbeatable. This guide will walk you through building a lean-to shed, focusing on simple plans and sustainable materials. Let's get started! [...]
Step-by-Step Wood Pallet Shed Build: Transform Old Wood into a Sturdy Shed
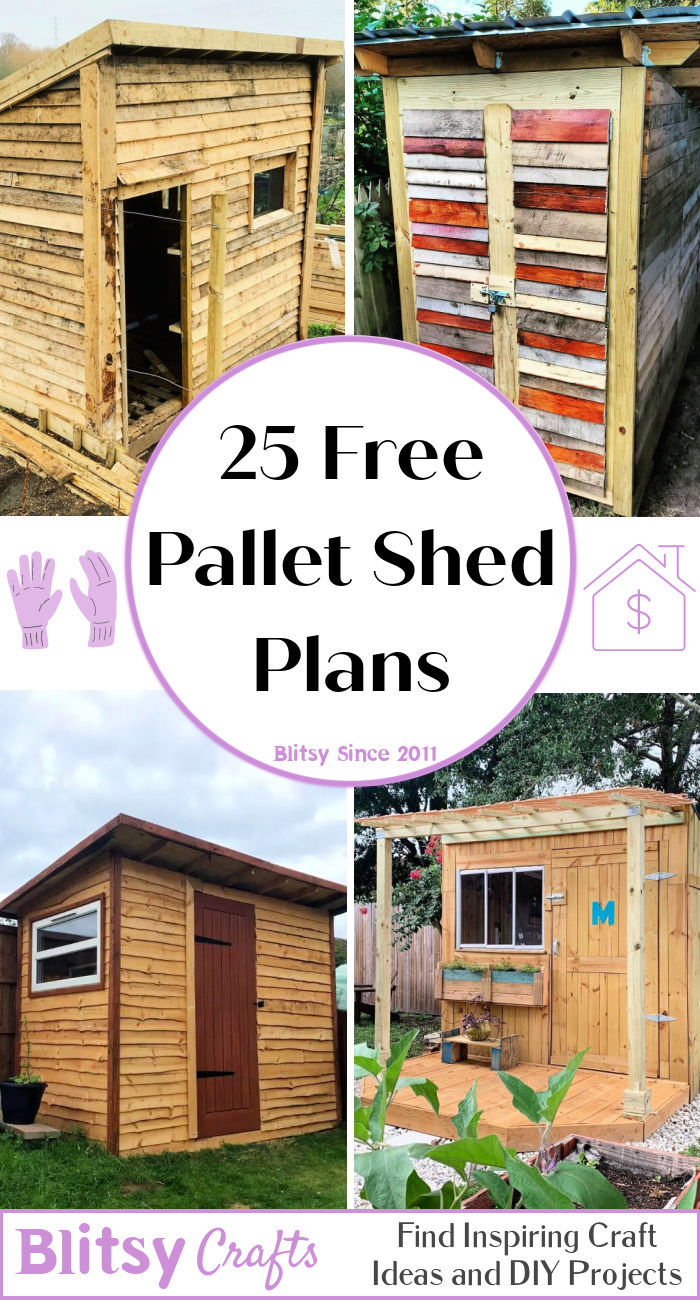
Step-by-Step Wood Pallet Shed Build: Transform Old Wood into a Sturdy Shed Hey there, fellow DIY enthusiasts! So you've got a pile of old wood pallets lying around and a yearning for a new shed? Fantastic! You're in the right place. This guide will walk you through building your very own sturdy shed using reclaimed pallet wood â€" saving you money and giving those pallets a new lease on life. Let's get started! Planning Your Pallet Shed: [...]
Subscribe to:
Posts (Atom)